Plastic bricks
Do you know that many plastics in the recycle bin cannot be recycled ? TWhat are the roadblocks in recycling plastic ? Can latest technology solve the problems and change the trend?
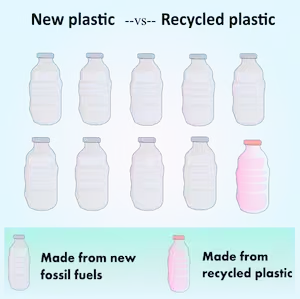
Plastic is an enormous problem.
New ecofriendly products make their way to supermarket aisles and online shopping sites every day.
But they have not reduced plastic production.
Production of single use plastic increases by 6 million tonnes every year.
Most of this comes directly from fossil fuels. Less than 10% of plastic is recycled globally. Many developed countries recycle lesser.
PET (Poly Ethylene Teraphthalate)
PET used in making bottles and containers is strong and durable plastic. Making new PET bottles from fresh fossil fuel is expensive than making PET bottles from recycled plastic. Used PET sells for a good cost. It is collected, sorted and recycled with interest.
Single use plastics
It is a different story for single use plastics. Single use plastic made from fresh fossil fuels is cheap. Recycling plastic involves collecting, sorting and cleaning it. This makes recycling expensive than new products. High costs make single use plastic end up in landfills with no takers for it.
Solution
Used plastic is affordable if it is not sorted. Which product can accomodate a mix of used plastics, without sorting ?
Answer to this lies in the construction industry ! Plastic bricks is one such new product.
Bricks made with unsorted plastic waste have many advantages. They cost less than normal bricks. They come in different shapes and sizes. They are light weight and long lasting.
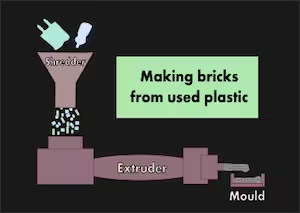
How is it made ?
Mixed, unsorted plastic waste is broken down into fine particles. This is called plastic sand. Plastic sand is made in shredders.
Clay, cement and fillers like shredded glass are mixed with it. It is heated and melted to form a cement like paste. The thick paste is squeezed out and sent to moulds. At this stage, it looks like cement or wet concrete. This is done in a machine called the extruder.
Extruded plastic cement is shaped in moulds to make bricks, roof tiles, floor tiles and pavers.
Some companies skip the extrusion process. A dry mix of plastic sand, river sand, cement, and other fillers are mixed thoroughly,
pressed in moulds and air dried to harden.
Benefits of plastic construction materials
It increases recycling of single use plastic. It extends the lifetime of plastic products.
It reduces usage of river sand which is otherwise the main ingredient in bricks. Mining of sand in river basins destroys natural ecosystems and affects water flow.
Plastic bricks reduce cement usage. Cement making involves harmful ingredients and has high carbon costs.
This is one recycling method that is here to stay. We hope to see more products built on this foundation.